How to manage vehicle downtime for fleet efficiency
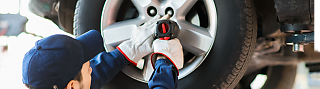
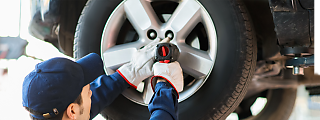
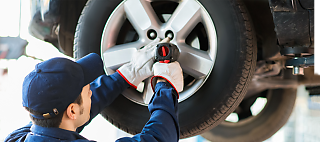
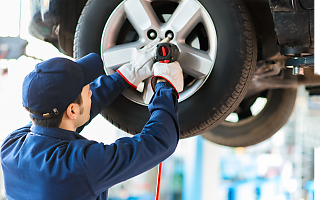
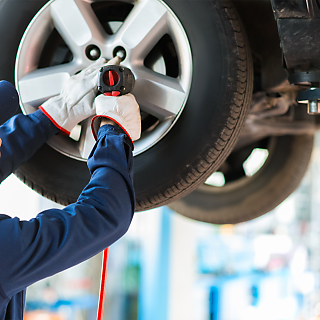
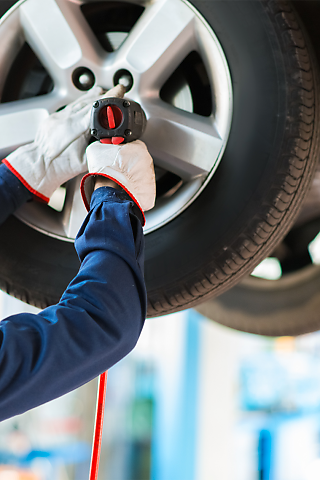
Whenever a fleet vehicle isnβt available for business use, itβs referred to as downtime. The most common cause of vehicle downtime is defects that require repairs or part replacements. Accidents or failure to pass inspections also contribute to downtime.
Limiting downtime is a key priority for fleets. Thatβs because vehicle downtime can erode productivity, leading to revenue and reputational losses. Itβs also important to mitigate downtime, since it can have an impact on your total cost of ownership (TCO).
Vehicle downtime can be planned or unplanned. Planned downtime is exactly what it sounds like: Youβve decided to keep your vehicle off the road for a set amount of time β itβs part of your operational schedule. Unplanned downtime is unpredictable and therefore unexpected. Like accidents, breakdowns are a type of unplanned downtime.
This guide explains how vehicle downtime can affect your business. It also offers strategies to reduce downtime, so you can operate efficiently and provide reliable service to your customers.
Understanding the cost implications of vehicle downtime
Itβs virtually impossible to overstate the ways in which vehicle downtime can eat into your bottom line. Letβs look at the direct and indirect costs associated with downtime.
- Financial impact: Direct costs like maintenance and repairs are part of your operational overhead. Indirect costs may be harder to track, even as they can contribute to a higher TCO. A survey from Northgate Vehicle Hire shows that LCV fleets in the UK lose a combined Β£2.4 billion per year due to downtime. That averages out to Β£800 per day in lost work for every unavailable vehicle. The same survey also shows that 47% of fleets face fines or penalties when their vans are off the road for a week.
- Reputational damage: Service reliability is essential in a competitive business landscape. Prolonged vehicle downtime can damage a companyβs reputation among customers, potentially leading to lost business. Fleets may work around this by renting vehicles, though this temporary fix can be a significant budgetary drain.
- Operational disruptions: Any fleetβs success depends on vehicle productivity. There will always be some amount of downtime β after all, you will need to schedule in maintenance and repairs. The trick is to operate as flexibly as possible, mitigating for planned as well as unplanned downtime.
Strategies to reduce vehicle downtime:
Proactively managing vehicle downtime is key to maintaining a productive, cost-efΒfective and safe fleet operation. By implementing the following four strategies, fleet managers can minimise unplanned disruptions and optimise their assets' uptime:
1. Conduct routine vehicle inspections
Regular inspections help you identify potential issues before they lead to vehicle failures, thereby reducing unexpected downtime and repair costs. Daily vehicle inspections help you stay compliant, meaning you can better avoid inspection or safety issues that could pull your vehicles off the road. Webfleetβs Vehicle Check app simplifies daily inspections for fleet managers and drivers. Discover how digitising vehicle inspections with the Vehicle Check app can increase your fleet efficiency.
2. Track and analyse vehicle health
By understanding vehicle health trends, you can schedule maintenance more efficiently, preventing costly breakdowns and reducing the time vehicles spend off the road. So how can you effectively track and analyse the condition of your vehicles? Fleet management software comes in handy, as it will provide the right business insights. With a solution like Webfleet, you can analyse vehicle data historically and in real time while also automating some of your maintenance tasks.
3. Monitor driving behaviour
Driver performance influences vehicle wear and tear, not to mention road safety. By keeping an eye on driving habits, you can assess whether coaching or training could benefit your team. Coaching drivers on limiting harsh braking and speeding supports vehicle longevity and helps prevent accidents, reducing downtime. Improving driving habits can also lead to savings on fuel, replacement parts and insurance premiums.
4. Schedule in regular maintenance
Routine servicing, also known as planned preventative maintenance, allows you to allocate expenses accordingly and keep your vehicles in top condition. Itβs therefore one of the best ways to prevent vehicle downtime: well-ΒmainΒtained vehicles are far less likely to break down, fail safety tests or cause compliance headaches.
Leveraging technology to minimise downtime
A fleet management solution like Webfleet gives you visibility over your fleet operations, making it easier to stay on top of maintenance, driving behaviour and vehicle health.
Smart scheduling with Webfleet
With smarter maintenance scheduling, you gain insights into the condition of each fleet vehicle. Create your preventative maintenance schedule with set dates and automated reminders. You can even base your maintenance planning on odometer data, minimising the chance of unplanned downtime.
OptiDrive 360 for enhanced safety
Well-ΒmainΒtained vehicles are safer vehicles. Keeping brake pads and tyres in premium shape, for example, means drivers have better control behind the wheel. But driving performance matters too. Webfleetβs OptiDrive 360 feature gives you the tools to evaluate driver scores and provide your team with actionable feedback.
Advanced diagnostic and trouble code notifications
As a fleet manager, you need to act promptly β before something goes wrong. In the case of diagnostic or engine trouble, Webfleet instantly sends you the relevant codes so you know which actions to take. Any related maintenance tasks will also be scheduled automatically.
Get it all done with Webfleet
This guide sheds light on the impact of vehicle downtime on fleet businesses, from financial losses to disrupted customer service. We hope the strategies outlined above help you can optimise your fleet's productivity and reliability.
Looking for more guidance on keeping your assets on the road and delivering exceptional customer service? Request a free consultation with one of our experts and see what you can achieve with Webfleet:
- Keep your vehicles in roadworthy condition
- Monitor driving behaviour and vehicle health
- Automate routine maintenance schedules
- Empower drivers with real-time feedback
- Digitise your workflow, including inspections
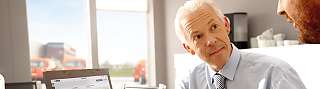

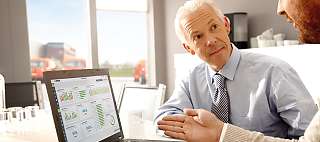
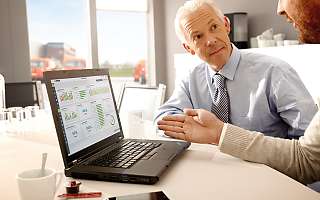
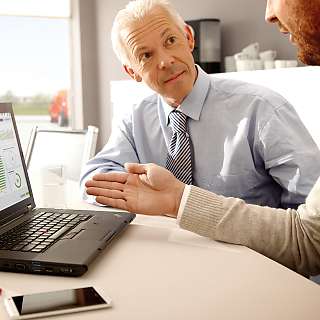
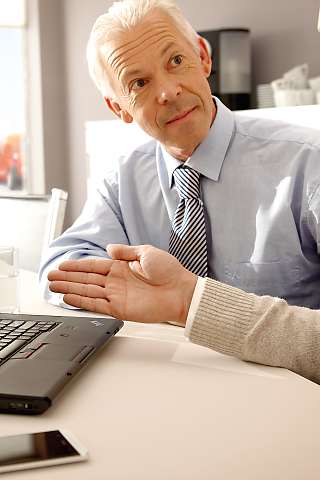
Your consent is required
In this section, external content is being embedded fromΒ .
To display the content, your consent is required for the following cookie categories:
- Targeted Advertising
- Analytics & PersonΒalΒization
- Essential
For further details, please refer to our privacy policy.Β If you are interested in how ###vendor_name### processes your data, please visit their privacy policy.